While competitors trap you in cloud ecosystems or demand expensive hardware, our technology delivers true sovereignty, radical efficiency, and breakthrough perception. Reimagine industrial AI: deploy machine intelligence directly from your CAD files to low-cost edge devices – with zero cloud dependency, no $10k accelerators, and uncompromised data ownership.
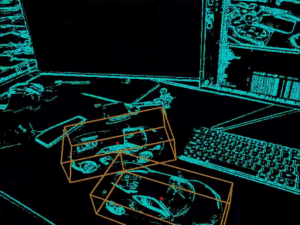
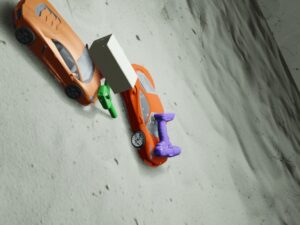
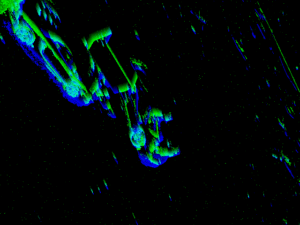
Your Unmatched Edge
We guarantee end-to-end sovereignty: your CAD data, training, and deployment stay entirely on your infrastructure, eliminating cloud lock-in. Achieve radical cost efficiency by running models on affordable hardware at a fraction of competitors’ power consumption. Most powerfully, leverage our event vision engine to unlock previously impossible environments – flawless operation in total darkness, extreme motion, and ultra-low-power (<1W) settings where conventional solutions fail.
How We Redefine Industrial AI
Transform CAD files into intelligent edge systems using physics-based rendering and automated synthesis. Train hardware-aware 2D/6D detection models that run locally without costly upgrades. Finally, harness event cameras to process sparse data streams for superior performance in conditions others cannot touch.